Why Welding Quality Matters in Structural Integrity
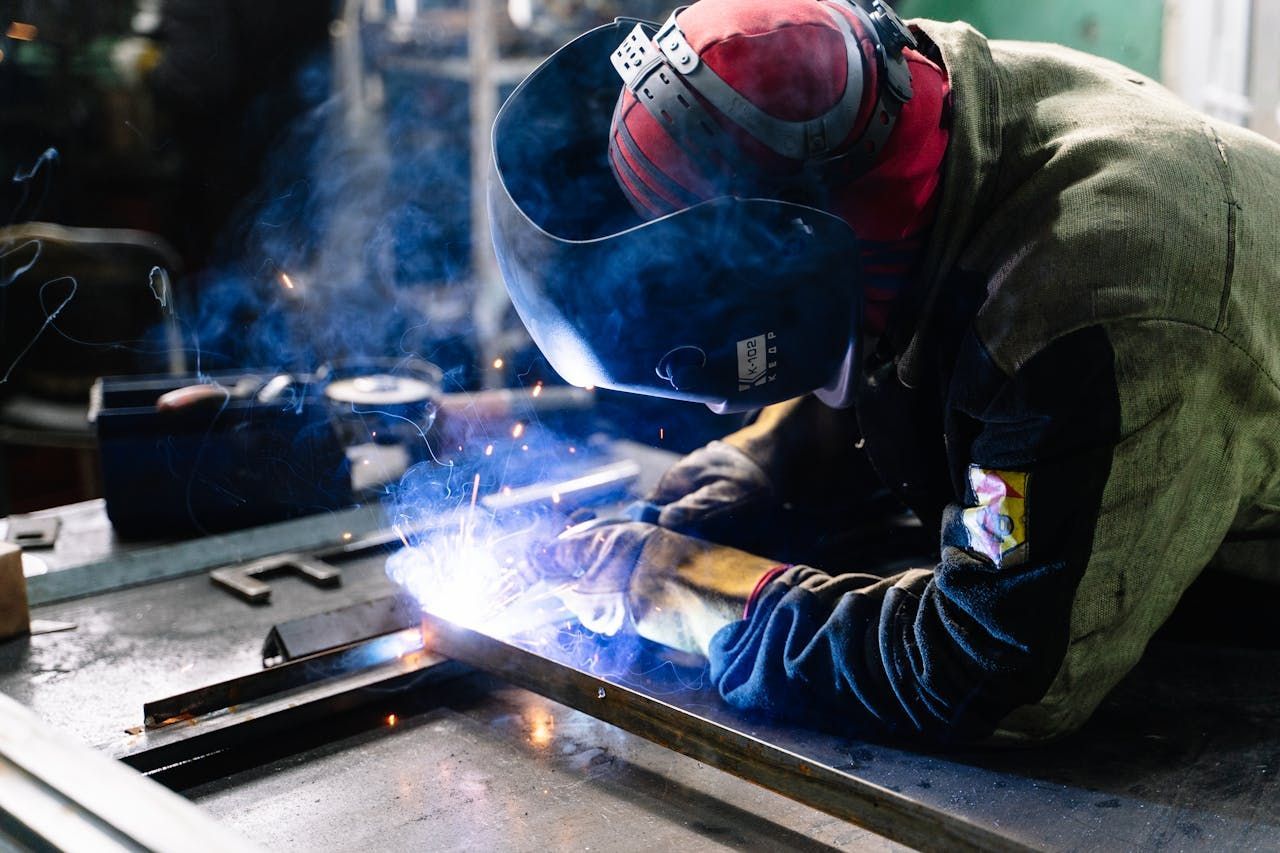
Welding isn’t just about fusing metal together—it’s the backbone of structural integrity. A strong weld holds up bridges, supports skyscrapers, and keeps industrial frameworks standing under immense pressure. However, when welding quality is compromised, the results can be disastrous. From weakened load-bearing joints to catastrophic failures, poor welding leads to costly repairs and serious safety risks.
The Role of Welding in Load-Bearing Structures
Every structure relies on a system of joints to distribute weight and absorb stress. A single weak weld can throw off the entire balance, leading to premature failure. When welds are executed with precision, they create seamless connections that reinforce stability, ensuring that buildings, bridges, and industrial equipment perform as intended—day after day, year after year.
The Consequences of Poor Welding
Subpar welding doesn’t just affect aesthetics; it weakens the structure at its core. Small defects can develop into major fractures under the right conditions, leading to unexpected failures. In high-risk environments—construction sites, industrial plants, transportation systems—there’s no room for error. Compromises in welding quality can result in substantial financial losses, injuries, and even fatalities.
Common Welding Defects and Their Impact
Here are some of the common welding issues you should know.
● Porosity: Tiny gas pockets weaken the weld, making it prone to cracking under stress.
● Incomplete Fusion: When metals don’t fully bond, the joint remains weak and unreliable.
● Cracks: These can form immediately or over time, leading to sudden structural failures.
● Slag inclusion: Non-metallic material trapped in the weld reduces strength and longevity.
Even the smallest defect can compromise an entire project, making precision welding a non-negotiable requirement.
Material Selection: More Than Just Metal
Not all metals behave the same under heat. Carbon steel, stainless steel, and aluminum have different melting points, expansion rates, and chemical compositions. Using the wrong filler material or welding method can lead to weak joints that crack under pressure. Experienced welders don’t just fuse metal; they understand how each material reacts, ensuring the right approach for every project.
How Welding Affects Corrosion Resistance
Welding isn’t just about strength—it also impacts how long a structure lasts. A poorly executed weld can accelerate rust and corrosion, especially in environments exposed to moisture, chemicals, or extreme temperatures.
Uneven weld beads and excessive heat input can create weak spots where rust spreads quickly, leading to premature failure. High-quality welding extends the life of metal structures, reducing maintenance costs and preventing unexpected deterioration.
Inspections: Catching Problems Beforehand
Welding quality is something you verify and there's no guesswork allowed. Rigorous inspections ensure that each weld meets industry standards before a project is completed. Testing methods like ultrasonic scanning, radiographic examination, and magnetic particle testing reveal hidden defects that could compromise integrity. Companies that invest in quality control prevent costly rework, avoid legal liabilities, and build trust in their structures.
Why Skilled Welders Matter
Welding is both a science and an art. A skilled welder understands metallurgy, heat control, and structural loads. They know when to adjust the technique, which materials require special handling, and how to create joints that stand the test of time. When projects depend on strength, precision, and longevity, hiring experienced professionals isn’t an option—it’s a necessity.
Need expert welding for your next project? At American Aerial Services, we deliver precision welding that keeps your structures strong and reliable. Trust our certified team for expert fabrication and inspections. Contact us today for welding solutions that last.
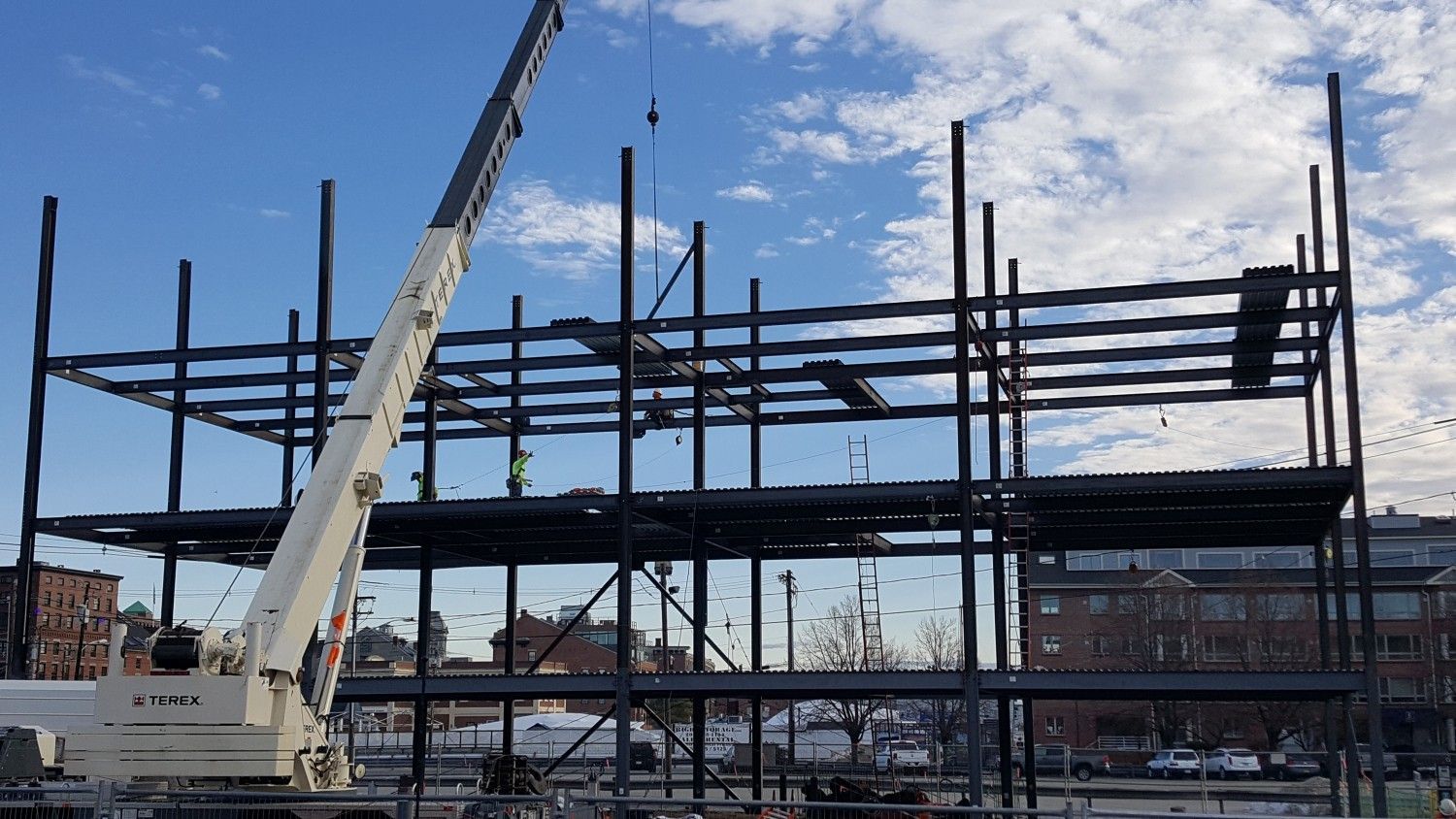
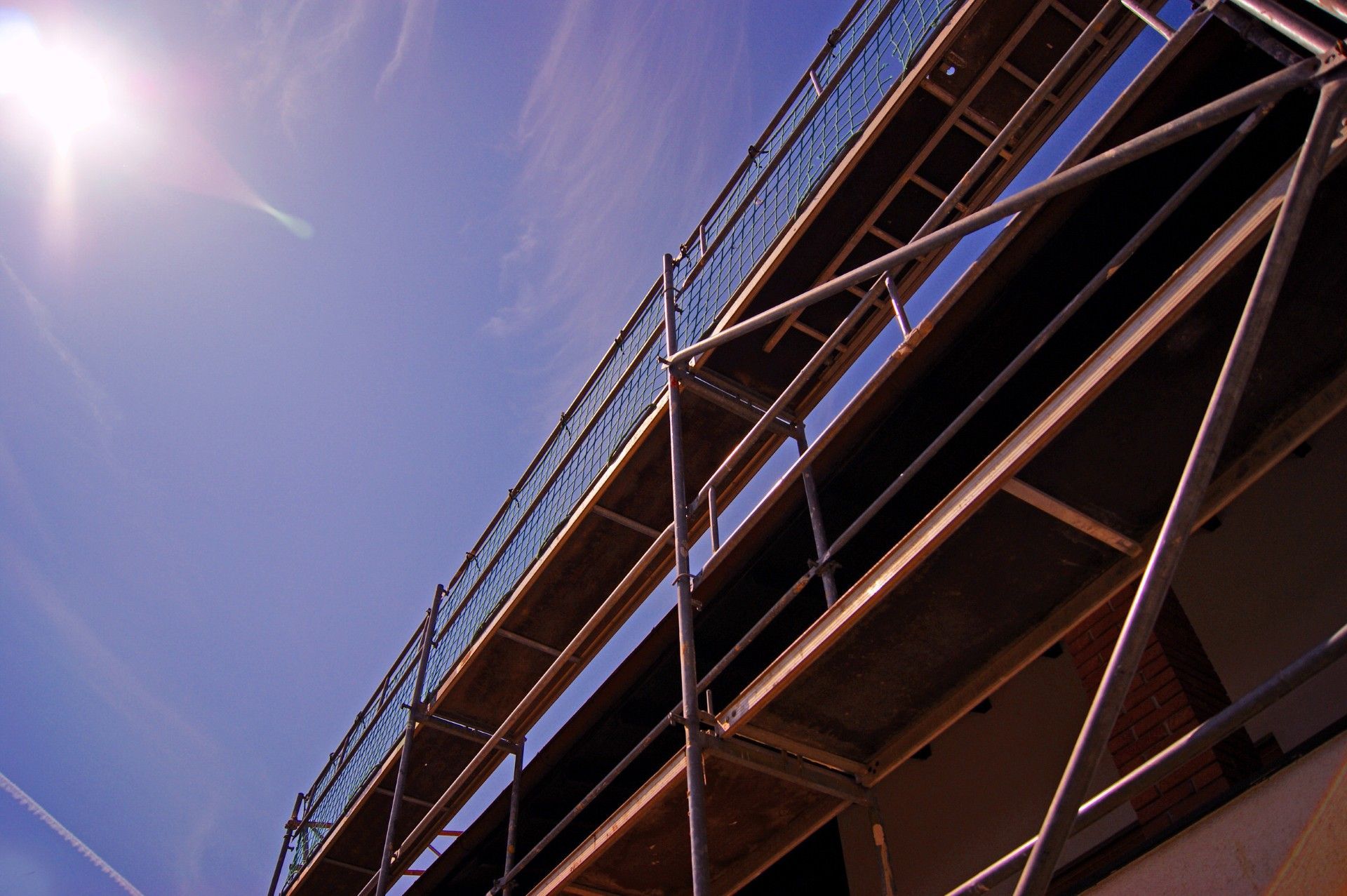
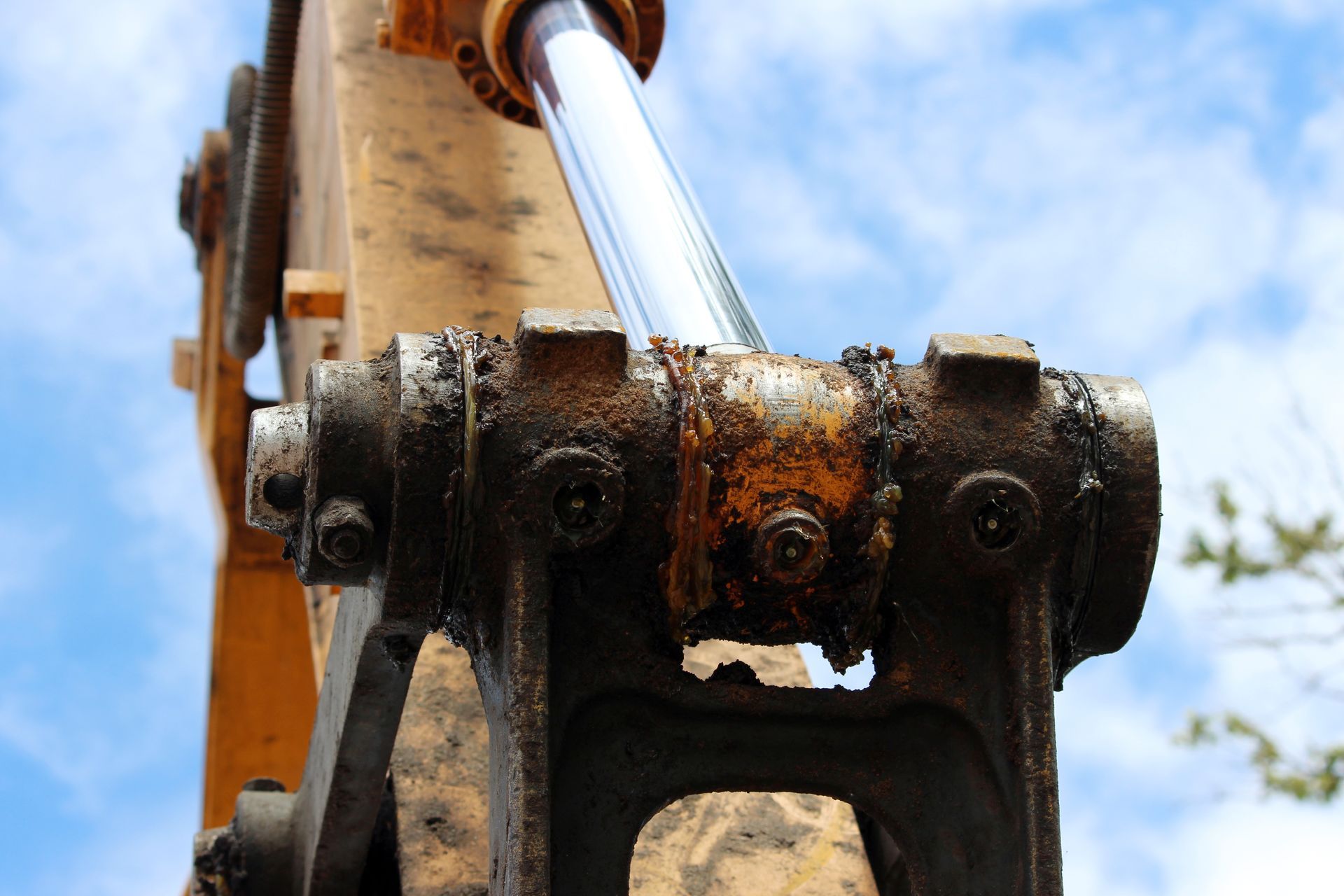
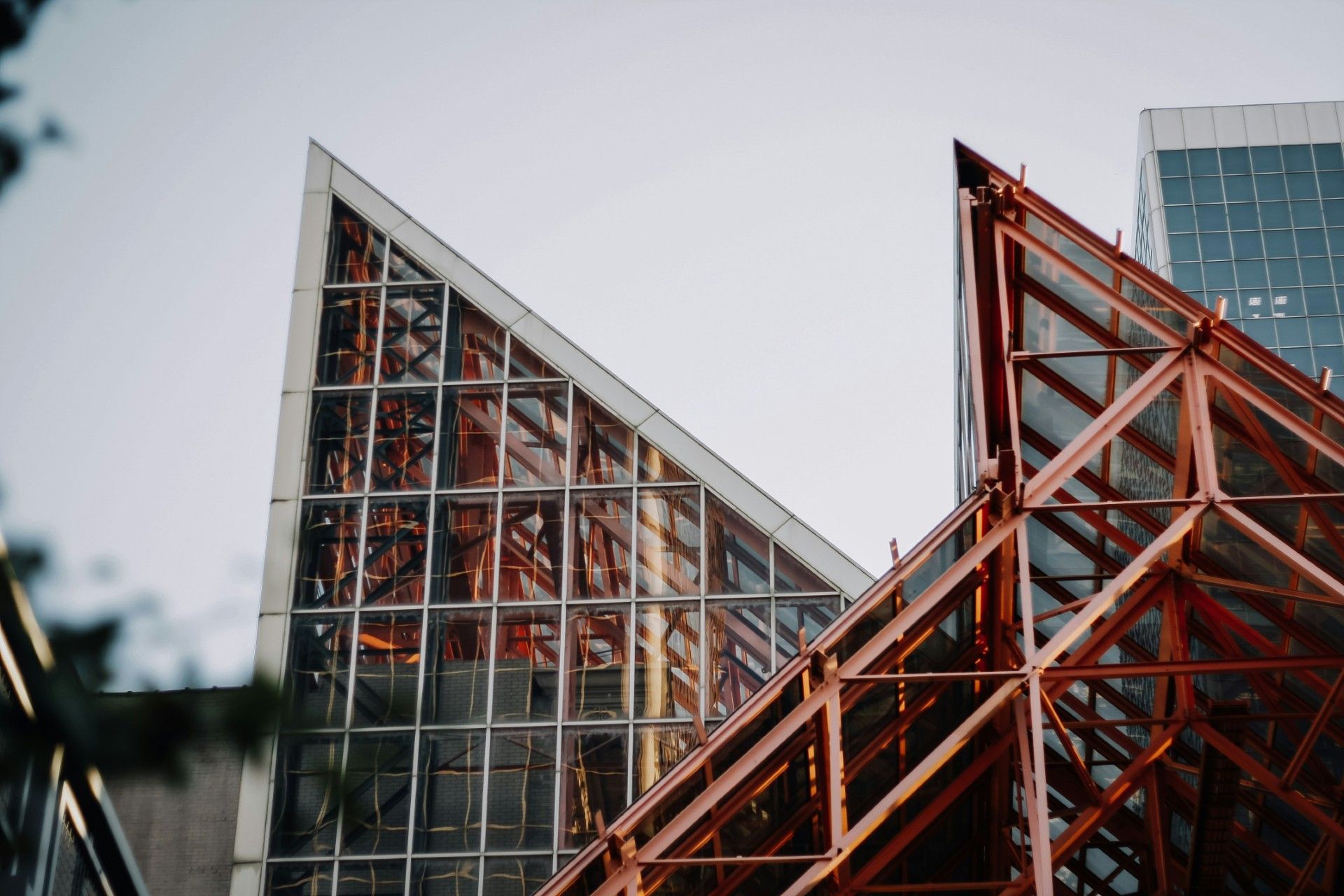
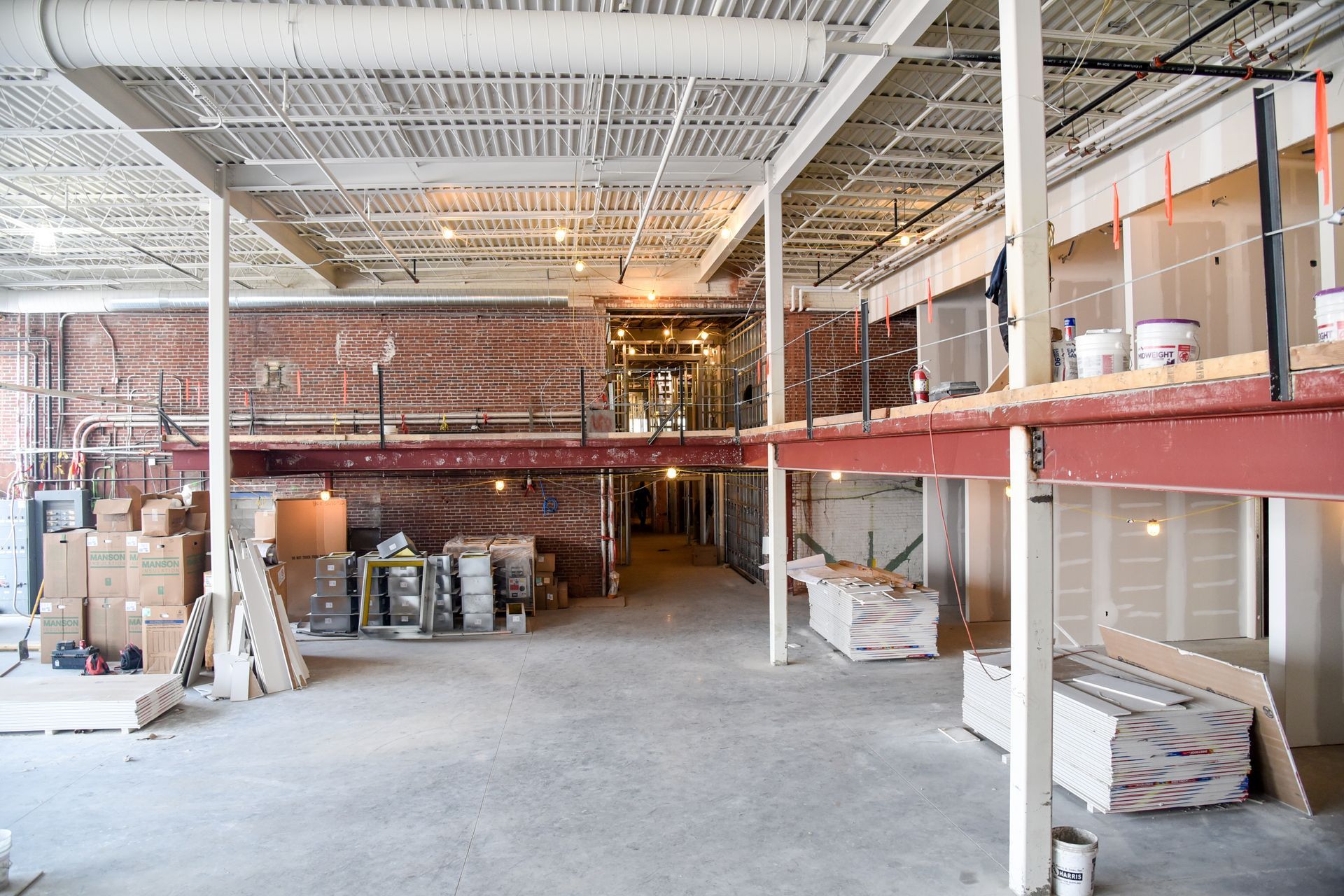

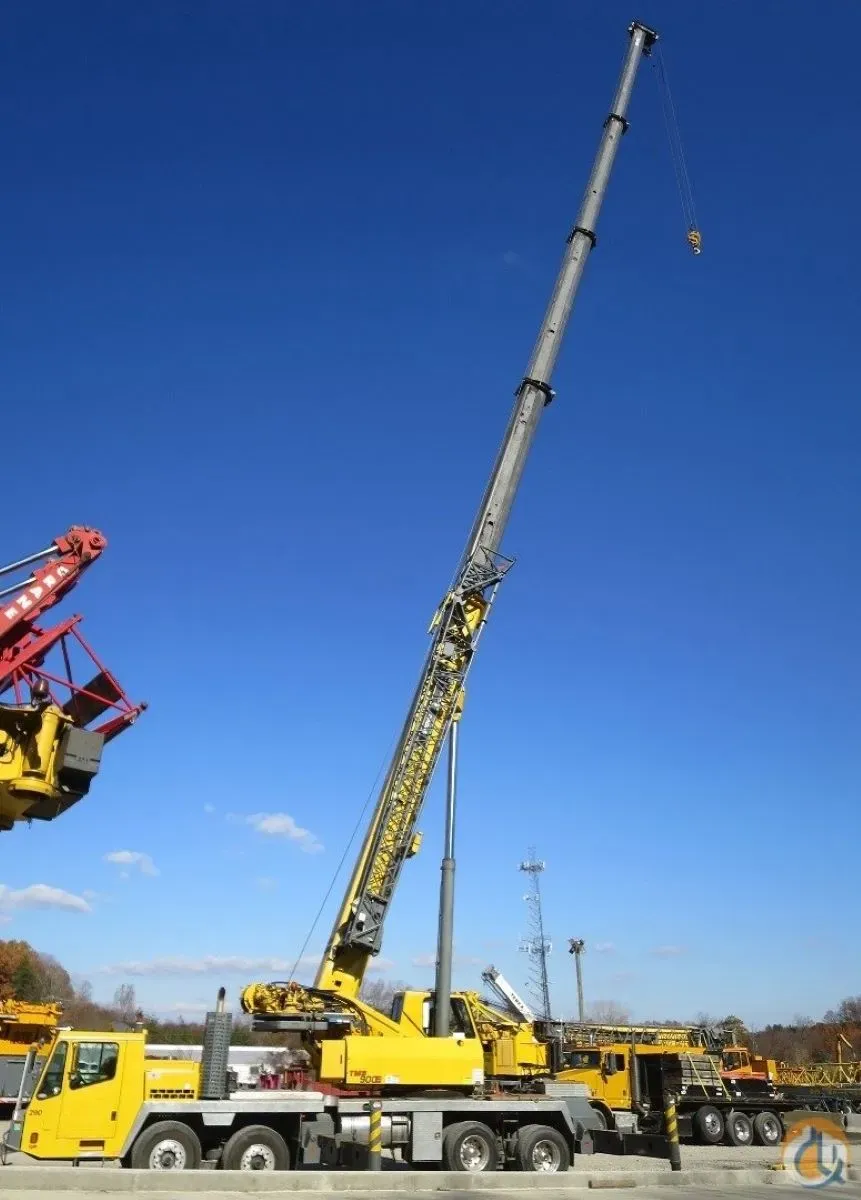
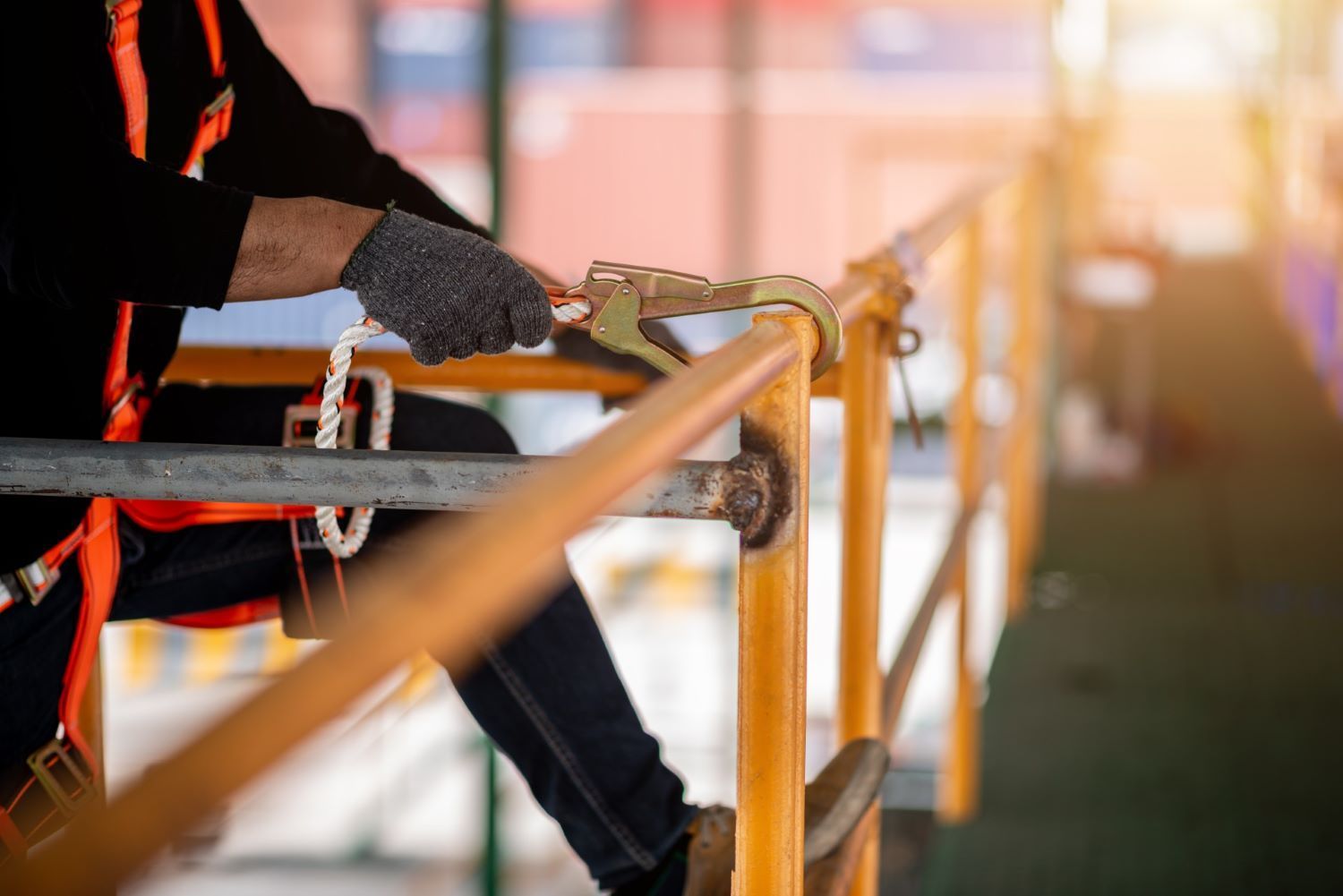